Predictive Maintenance: Fluid Flow Measurement Testing
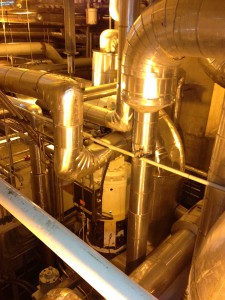
Operating off of a preventative maintenance plan can often result in untimely repairs
Hydraulic control system failures are expensive due to the costs and time associated with locating and repairing failed components. Preventative maintenance is imperative as is timely identification of components that have failed. Operating off of a preventative maintenance plan can often result in untimely repairs.
Using Fluid Flow Measurement Testing, a non-intrusive predictive maintenance approach, you are given insight into the actual condition of your electrohydraulic control system through the isolation of failed components.
Benefits
- Pre-outage testing allows for better budgeting and overall outage planning.
- Post-outage testing verifies that all repairs were done to OEM specifications resulting in an efficiently operating system.
How It Works
- Non-intrusive measurements of internal leakage are taken to assess the level of wear on critical surfaces and to detect bad seals.
- Isolation of failed components without interruption of system operation.
- Our trained technical team comes on-site
- Develop trend analysis and test data in preferred flow units.
On-site Services Offered
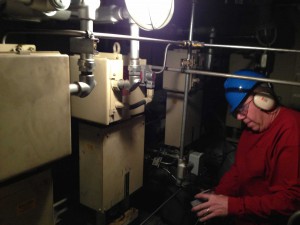
Our highly experienced team are available to solve all your problems both on and off site
Periodic Flow Testing
Intended to develop operating trends and aid in scheduling of preventative maintenance. This test consists of periodic measurement of internal leakage of individual components. Variations of the internal leakage overtime may indicate normal wear, fluid contamination, or damaged seals.
Component Isolation Testing
Intended to isolate a bad component(s) in an otherwise healthy system. Pump cycle times, excessive amp draw, and pressure loss, may indicate a failure within a hydraulic system.
EHC Troubleshooting
When preliminary research is needed to identify system issues and additional expertise is required to determine EHC pressure problems, our technical team is available.