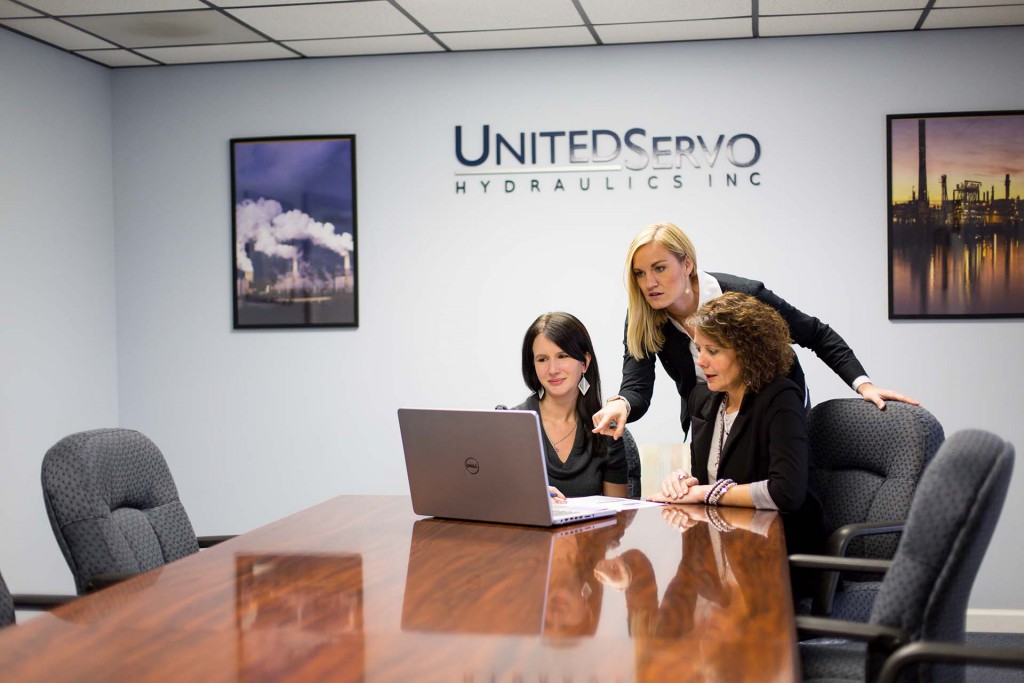
Pre-Outage Planning
Pre-Outage Planning
Pre-outage planning and unit arrival is coordinated with a designated Account Executive who maintains detailed records of project deadlines and requirements.
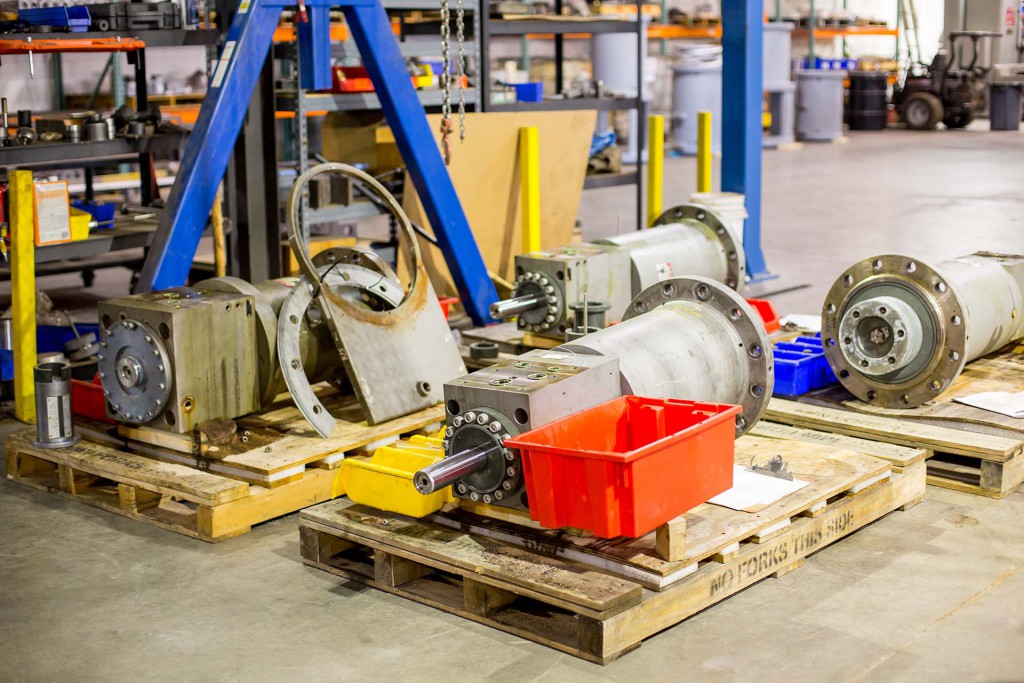
Unit Check-In
Unit Check-In
Upon arrival, each unit and component is photographed and identified by serial number. Your Account Executive will notify you that the units have arrived and confirm that the order arrived in its entirety.
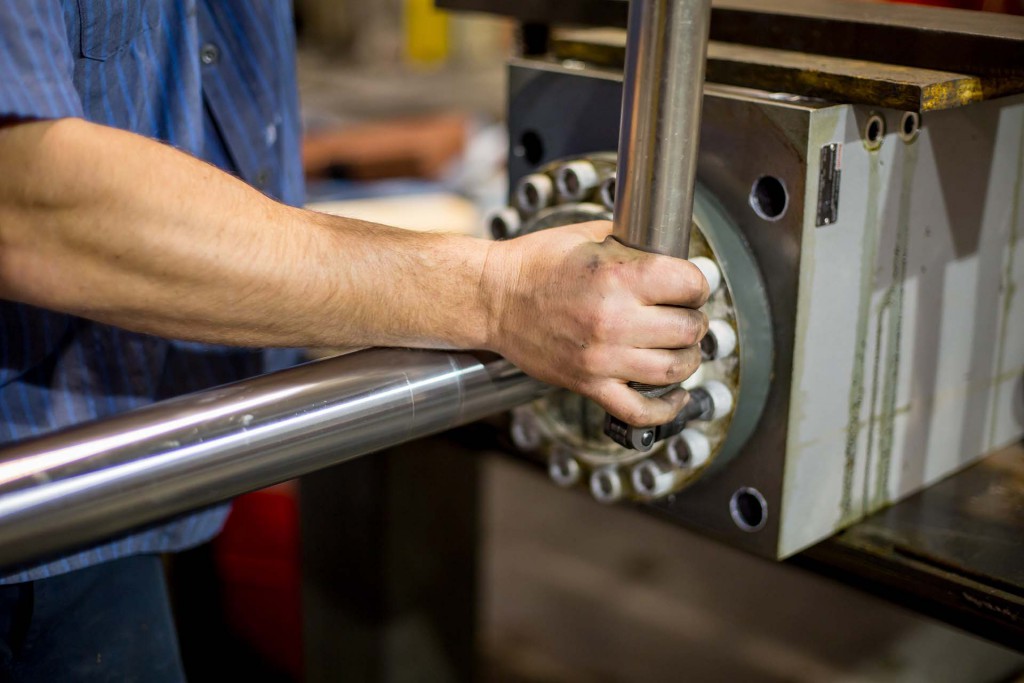
Dis-assembly & Part Inspection
Dis-assembly & Part Inspection
Each component is removed and visually inspected. An inspection of all manifolds and orifices is performed. Each part is inspected and photographed to uncover signs of wear, pitting, corrosion, and grooving.
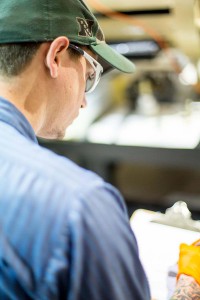
Repair Recommendations & Pricing
Repair Recommendations & Pricing
Soon after parts inspection, final pricing and repair recommendations are presented to the customer for final approval. Through careful measurement, our team determines when part replacement is necessary for OEM specification adherence.
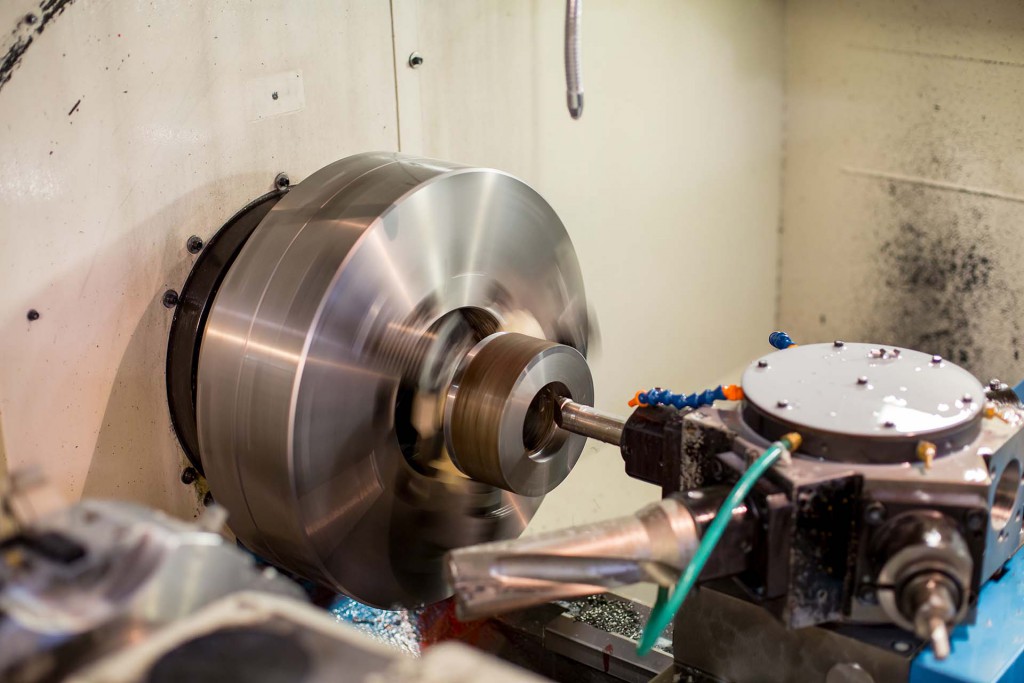
Replacement Parts
Replacement Parts
When replacement parts are required, we look to our spare component inventory along with our complete machine shop to quickly supply the needs of your order. Through pre-outage planning on critical outage timelines, replacement parts can be order prior to the units arriving.
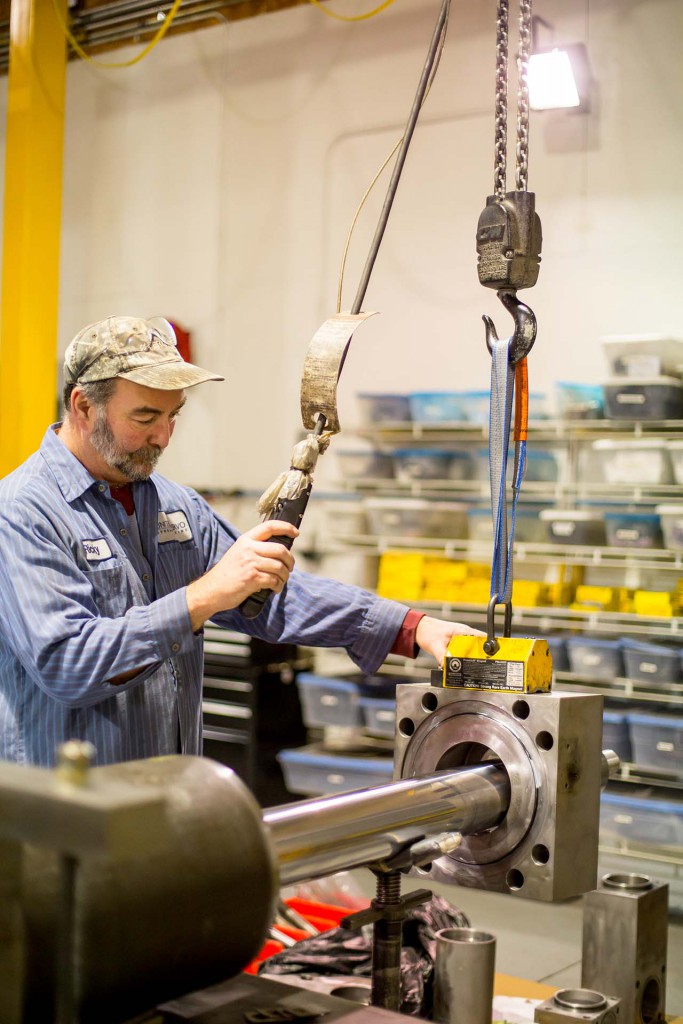
Cleaning & Reassembly Component
Cleaning & Reassembly Component
Each unit undergoes chemical or ultrasonic cleaning. Seals and O-rings are replaced using Viton only and tie rod and fastener torque is verified
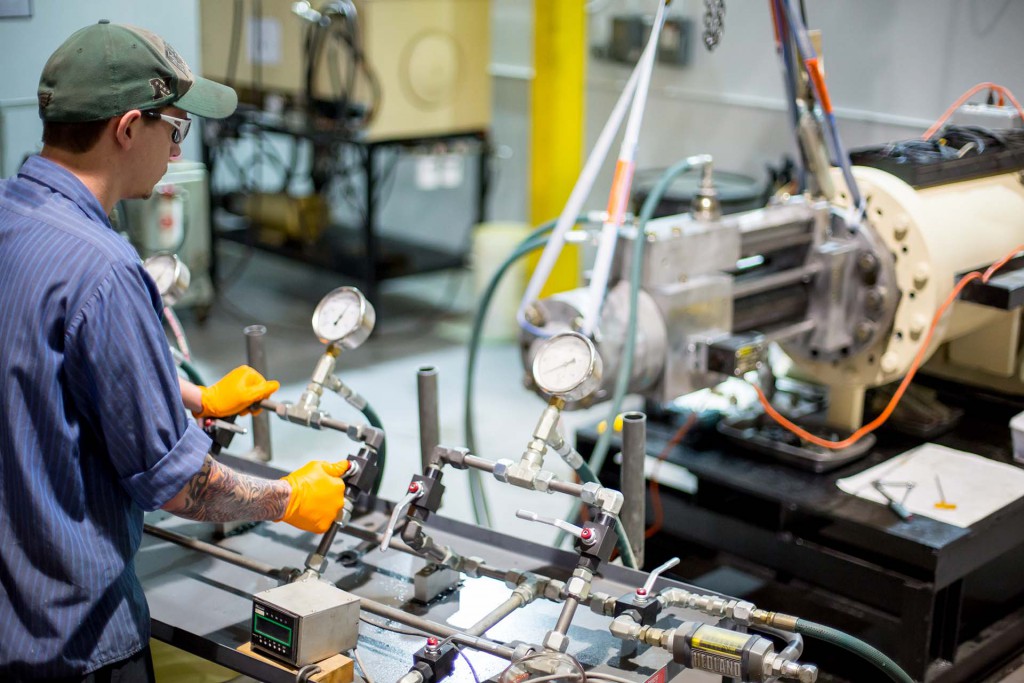
Final Test & Paint
Final Test & Paint
Units are pressure tested using EHC fluid at a minimum of 2000 psi, verifying operation, and inspection for leakage. Fluid is drained and all fittings are capped. The unit is prepped and painted.
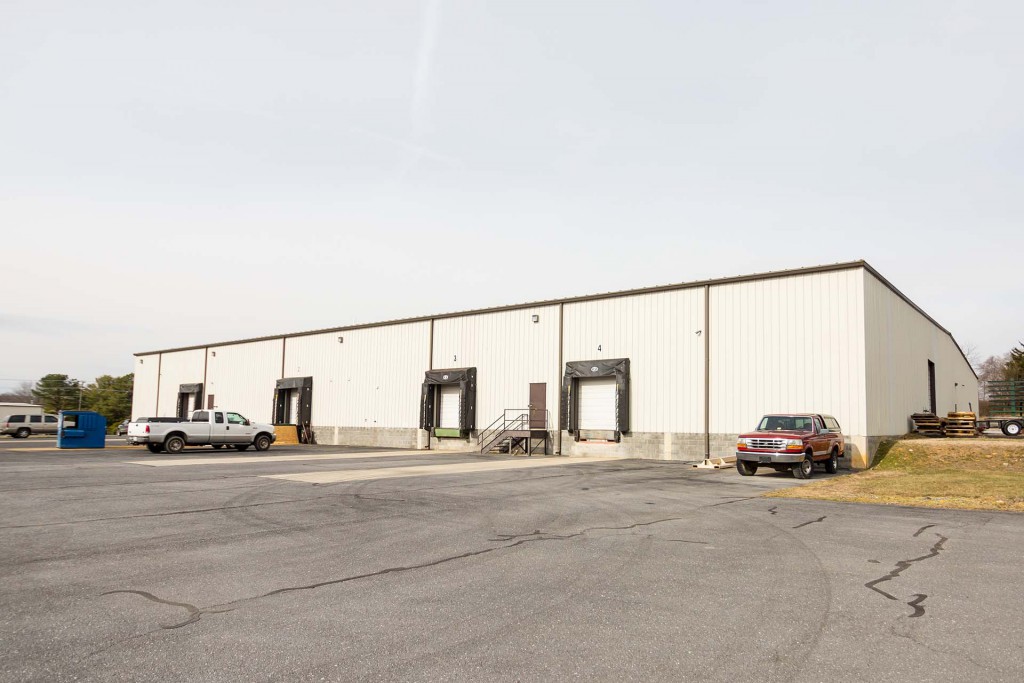
Final Test Reports & Unit Delivery
Final Test Reports & Unit Delivery
All units are packaged securely for shipment and final test reports data is presented for the entire project. Logistics are arranged by United Servo when requested. United Servo will maintain records of your assembly components and condition for future orders and unit performance trending.